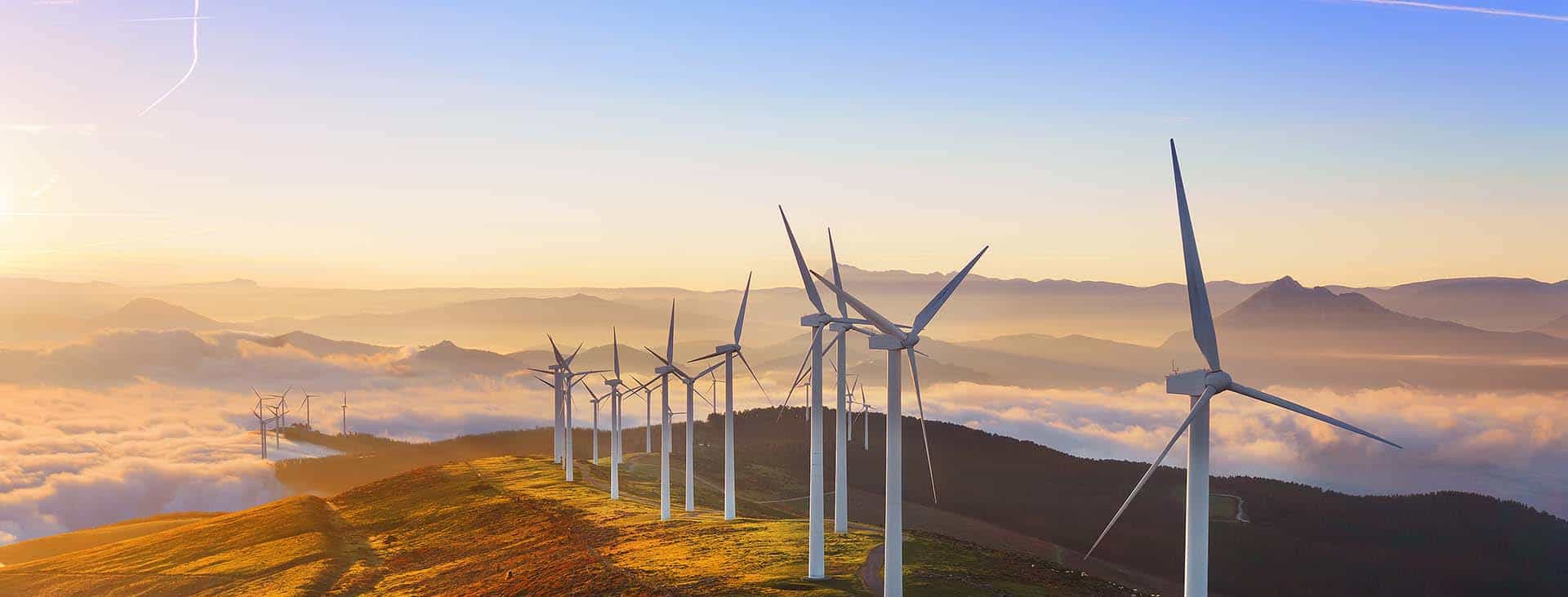
Aluminum vs. copper wire windings in transformers
Transformer manufacturers and installers have been discussing the pros and cons of copper versus aluminum wire windings for years. Many people believe copper is superior to aluminum. This is because decades ago, improper termination on aluminum windings caused house fires. However, proper termination eliminates that threat.
There are multiple advantages and disadvantages to both copper and aluminum windings. We explore a few here.
Aluminum winding pros and cons
Pros
- Greater heat storage. During short time overload, heat is stored within the transformer’s windings. Aluminum windings can store approximately 2.3 times greater heat per pound when compared to copper windings.
- Stronger moisture/corrosion resistance. As published in the NEMA Magnet Wire, publication no. MW1000-1973, section MW-36-A, an aluminum-manufactured transformer is rated to provide insulation at 220° C. Section MW-36-C rates the same insulation on copper at 200° C. A higher insulation rating for aluminum wire results in less deterioration of electrical insulation.
- Dramatic eddy current reduction. Aluminum windings drastically reduce eddy currents found in wire wound transformers. In addition, due to a reduction in the volts-per-turn, aluminum results in better short circuit capacity.
- Better harmonic management. Harmonics result in heat build-up and manifest on the conductor surface. Aluminum provides a greater surface area, which allows the transformer to better handle excess heating caused by harmonics.
- Less mechanical stress. Due to more easily conforming to the shape of the winding, aluminum causes less mechanical stress as it’s being applied to the coils.
- Exterior oxidization. While zero oxidation on transformers is ideal, oxidation can not always be avoided, so the least amount of oxidation is favored. Aluminum only oxidizes where it’s exposed to air, but once oxidation starts on copper materials, the copper will oxidize all the way through, including areas not exposed to air.
- Stable pricing. Historically, aluminum pricing has remained stable in the marketplace, which allows for easier cost forecasting when quoting transformers.
Cons
- Greater electrical connection difficulty. Aluminum expands approximately one third more than copper when put under heat. Combined with the fact that aluminum oxidizes when exposed to air, electrical connections are more difficult to create with aluminum windings. Extra precautions, requiring more manual work, must be taken to ensure the electrical connections are airtight.
- Additional material required. Due to aluminum’s electrical properties, aluminum wire sizes are two to three sizes larger than copper wire sizes. This can result in a larger transformer, which may conflict with space restrictions.
- Additional maintenance. A transformer manufactured with aluminum windings requires greater maintenance than a transformer manufactured with copper windings, as aluminum oxidizes more quickly.
- Easier connection and joint oxidation. Aluminum oxidizes quite readily when exposed to air. While aluminum oxidation will not travel through the transformer, as oxidization only occurs on aluminum surfaces exposed to air, copper does have greater oxidization-resistant properties.
Copper winding pros and cons
Pros
- Less material required. Due to the nature of copper’s electric conductivity, copper wire sizes are two to three times smaller than aluminum wire sizes. Although copper maintains a greater weight than aluminum, the smaller wire sizes result in a smaller transformer. A smaller footprint is especially ideal for industrial control panels, where real estate becomes quite costly.
- Easier electrical connections. Electrical connections are far easier and simpler to form with copper. This is because the chloride, oxide and sulfide properties found in copper metal are simply more conducive to electrical connections.
- High electrical conductivity. Copper metal contains much higher electrical conductivity capabilities than aluminum, with some sources stating that aluminum contains only 61% of the conductivity of copper. This can lead some to believe copper windings possess greater energy-efficiency properties, however, aluminum winding energy losses can be very similar to copper when the wire sizes and core losses are varied accordingly.
- Less maintenance and easier manufacturing. Due to copper’s properties, copper transformer windings provide an easier weld during the manufacturing process. Once manufactured and installed, a transformer that has copper windings also requires less maintenance.
- Does not easily oxidize. Copper possesses a greeter resistance to moisture-corrosion/oxidation. While copper does oxidize all the way through once the oxidation process is started, oxidation doesn’t occur as easily.
Cons
- Complete oxidation. When the oxidation process begins, copper will oxidize completely, similar to steel. Whereas aluminum will only oxidize on surfaces exposed to air, copper will oxidize all the way through. This results in faster transformer deterioration when transformers are manufactured with copper windings.
- Volatile cost. The cost of copper can greatly fluctuate, from extremely cost-effective to extremely costly. Non-stable prices result in complications when attempting to forecast a transformer cost, as well as product transformers in the most cost-effective manner.
The best winding material for your application
The advantages and disadvantages highlighted when comparing aluminum vs. copper wire windings can help determine the transformer specs your particular application requires. To learn more about whether aluminum or copper windings is best for your application requirements, contact us today.